Stock management is an indispensable process in today’s integrated logistics sector. It covers all operations within a distribution centre. In the following sections, we will explain everything you need to know about this process.
OUR SERVICES
STOCK MANAGEMENT
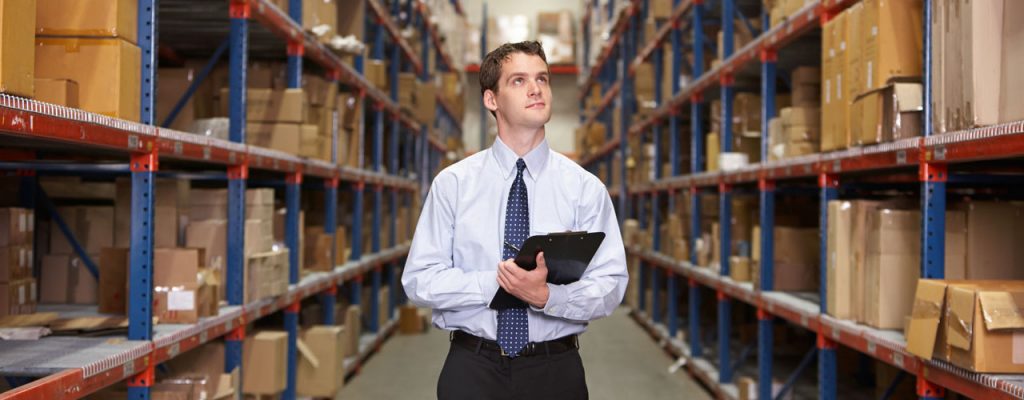
CONTROL, OPTIMISATION AND STOCK MANAGEMENT: HOW DO THEY DIFFER?
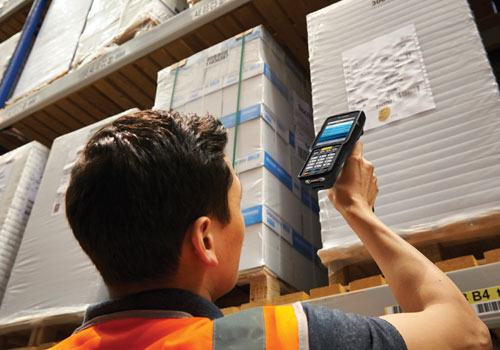
There are some differencesbetween what is known as stock control, stock optimisation and stock management, although they are processes that take place within a logistics company, they are distinct.
Stock control refers mainly to the availability of the different products inside the warehouse. In this way, you can control the input and output of materials more efficiently.
Optimisation, on the other hand, is about improving service. Optimisation is about increasing the company’s productivity. By optimising, you can be more efficient to make a higher profit.
Finally, stock management is a more complex process. It covers different tasks such as the organisation within the warehouse, the traceability of the products. This avoids errors and improves productivity.
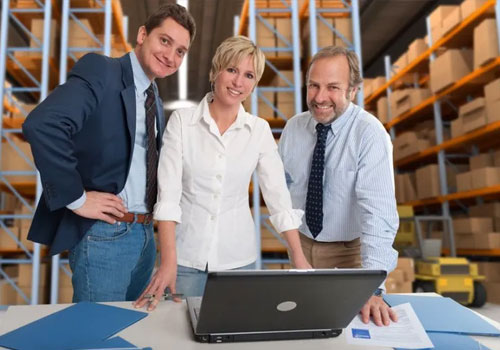
CONTROL, OPTIMISATION AND STOCK MANAGEMENT: HOW DO THEY DIFFER?
Within stock management, there are different types of stock management. In the following, we will describe the different types that can be found within an integrated logistics company.
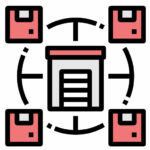
SAFETY STOCK
The safety stock is the stock that we must have in case of an imponderable. It is used to keep stock on hand in case there is a shortage of product or if the customer orders a large quantity.
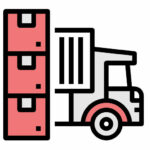
ACTIVE OR NORMAL STOCK
In stock management, active or normal stock is the stock that is usually found in the warehouse. That is to say, that which is regularly moved out of the storage centre.
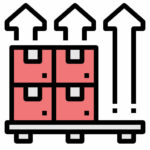
MAXIMUM STOCK
In the case of maximum stock, it is the maximum quantity of a certain product that can be stored in a warehouse.
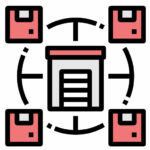
MINIMUM STOCK
Minimum stock, in stock management, is the opposite of the previous point. In this case, it is the minimum quantity of a product that we can store inside the tank.
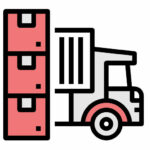
SURPLUS STOCK
In terms of surplus stock, we refer to those products that cannot be sold. Through stock management, we can find a good outlet so that it does not take up space in the warehouse, thus making a profit.
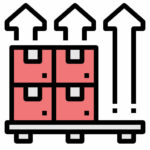
ZERO STOCK
Finally, we find the zero stock. In this case, just theright amount of the product to be used is stored in the tank. This may carry some risk of not being able to meet the demand in case it rises.
MOST COMMONLY USED MODELS IN STOCK MANAGEMENT
Within stock management, there are different types of stock management. In the following, we will describe the different types that can be found within an integrated logistics company.
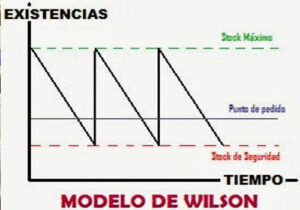
STOCK MANAGEMENT WITH WILSON MODEL
The first model is known as Wilson. In this case, companies have a fixed cost in advance that does not depend on the product. In this case, the order is of large dimensions to save transport costs.
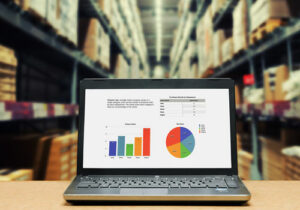
STOCK MANAGEMENT WITH ABC MODEL
Another model of stock management is ABC. In this case, the goods are classified with different letters in order to have a better order inside the warehouse.
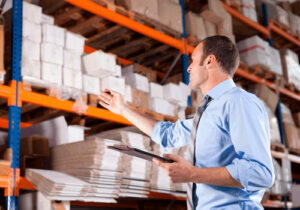
GOODS CLASSIFIED UNDER LETTER A
Goods that are labelled with the letter A are those that are of the greatest importance. In turn, they have a higher value.
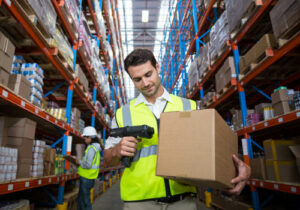
GOODS CLASSIFIED UNDER LETTER B
In the case of goods marked B, they are of medium importance. In these cases, the control is less thorough than for A-marked goods.
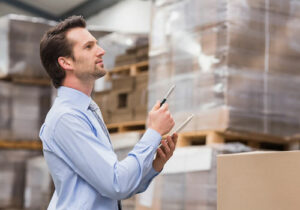
GOODS CLASSIFIED UNDER LETTER C
Finally, those marked with the letter C are the least valuableto the company. Control is not as high, but it is always important to know what is inside the warehouse.
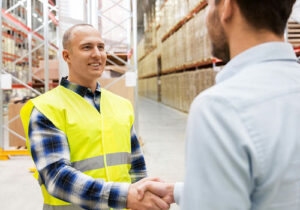
JUST IN TIME MODEL
This model is based on cost reduction. The strategy here is to order the quantity of product in relation to demand. That is to say that it is just what is necessary.
OBJECTIVES OF INVENTORY MANAGEMENT
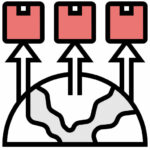
Matching stock to demand effectively: The important thing is to have a good strategy for matching the quantity of product to demand. In stock management, we find the application of big data to improve organisation and increase efficiency.
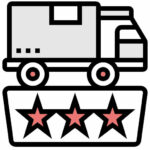
Ensuring quality of service: Good service is the key to a logistics company. It is important to deliver products on time. Through stock management, you can use merchandise tracking to prevent errors that cost customers.
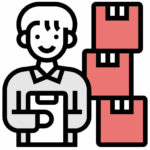
Lowering the cost of storage: A key objective is to lower costs. For this, it is very important to design strategies in advance to optimise resources in order to considerably lower costs and increase productivity.
How can we
help you?
service tailored to your needs.
+34 651 80 25 62
digital@logistock.es